The Hidden Cost of Chaos in Flat Glass Fabrication
Glass
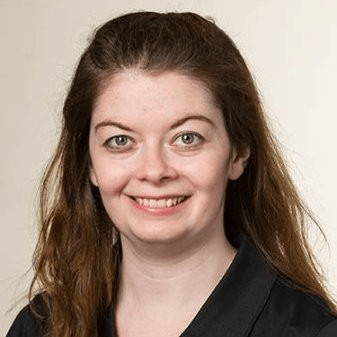
Ryan Anderson
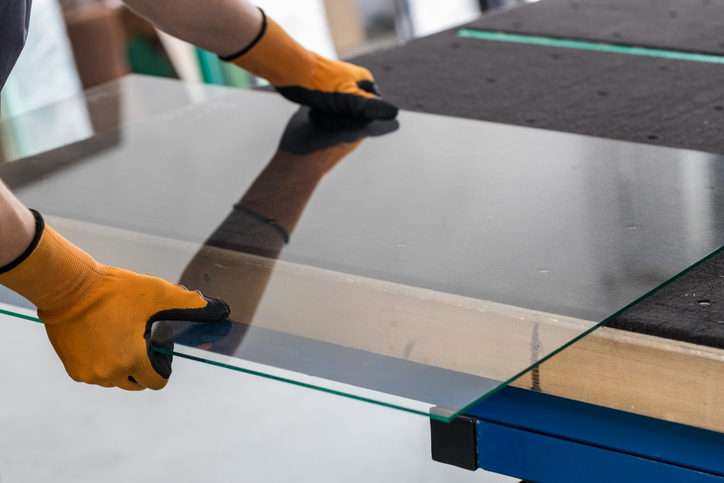
Walk into most flat glass fabrication facilities and you'll see a business in motion - orders coming in, teams working overtime, tempering furnaces and CNC work centers humming. But beneath the surface, there’s often a familiar tension: the feeling that no matter how hard everyone works, it’s never quite enough. Something’s always being chased down - a missing lite of glass, a delivery deadline, a rush remake to walk through the entire workflow. Growth feels possible, but distant. Worse, it feels like it demands more and more from a team that’s already stretched thin.
It’s not a lack of effort. It’s the hidden cost of chaos.
In flat glass, no two jobs are the same. That’s what makes the work so valuable - and so difficult to standardize. But without the right systems and structure, that variability becomes volatility. A quote that doesn’t reflect material constraints could shut down the tempering furnace when the lite falls through the rollers. A production delay becomes a missed delivery. A missed delivery becomes a lost customer.
And just like that, you’re not building your business - you’re holding it together.
What’s often missed in this cycle is the slow erosion of potential. When operations are built on workarounds and spreadsheets, growth isn’t just slowed - it’s distorted. New hires take months to ramp up because the process lives in someone’s head. Chaos ensues when the scheduler or shipping logistics coordinator takes vacation or sick leave. Sales are limited to what your team can manually price. Leaders spend more time reacting than refining. And even your best people burn out - not because they don’t love work, but because they’re stuck in a system that can’t scale.
But here’s the good news: this isn’t inevitable.
Across the industry, forward-thinking fabricators are choosing to move beyond survival mode. They’re reimagining what daily operations could look like with fewer handoffs, fewer errors, and more clarity from quote to delivery. They’re building businesses that grow not just in size, but in resilience - because every part of the operation is working with the same data, toward the same goals.
This shift isn’t about big machines or bigger budgets. It’s about rethinking how workflows, and how your team supports each other instead of compensating for disconnected systems. It’s about taking back time to focus on quality, service, and scale.
In our free business playbook, Chaos to Control: Scaling Flat Glass Production with Confidence, we explore the root causes of daily inefficiencies - and how to fix them. Through real-world insights and a step-by-step approach, the guide shows how to eliminate the friction that slows your business down and build the structure that allows it to speed up.
You’ll learn how to:
- Spot the invisible bottlenecks hiding in your workflow
- Align your team around clear processes - not tribal knowledge
- Create space for sales to grow without overwhelming operations
- Move from firefighting mode to focused, strategic execution
This is more than a guide - it’s a roadmap for leaders who are ready to stop working harder just to keep up, and start building a business that runs better.
Ready to break free from chaos?
Download the playbook today and discover what scalable success looks like when every part of your business works together.